BGA Rework Station
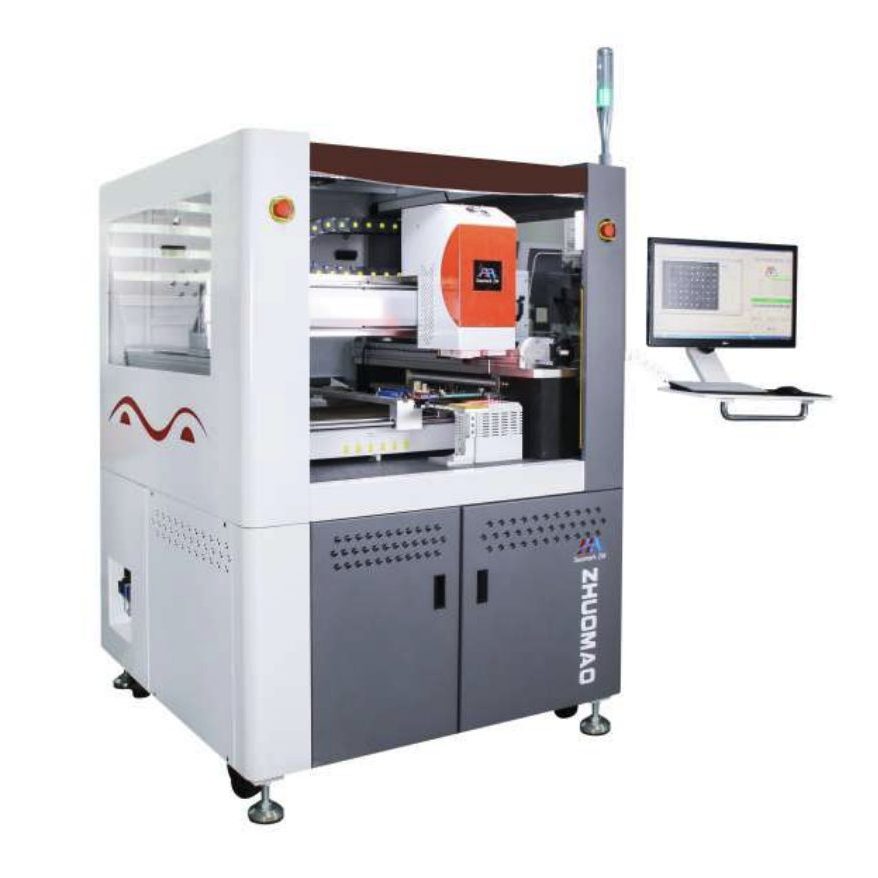
ZM-R8650C BGA Rework Station
Call for price and availability
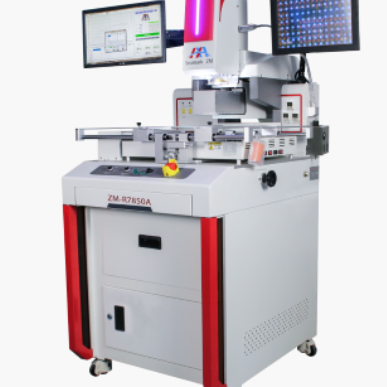
ZM-R7850A BGA Rework Station
Call for price and availability
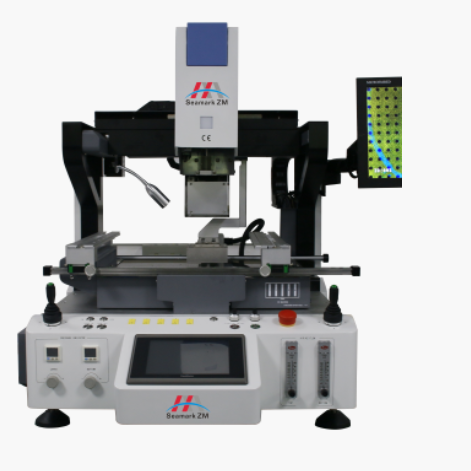
ZM-R7830A BGA Rework Station
Call for price and availability
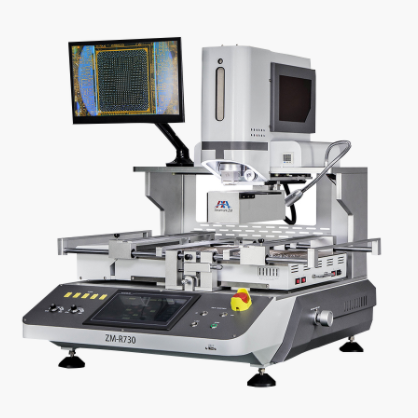
ZM-R730A BGA Rework Station
Call for price and availability
What Are BGA Rework Stations?
Technicians modify printed circuit boards (PCBs) with surface-mounted devices and ball grid array (BGA) packaging. We call this workspace system a BGA rework station. It's also referred to as a surface mount technology (SMT) or surface mount device (SMD) rework machine. These stations feature:
- Size and volume variations: A BGA station's features determine the size of the circuit board and the volumes or types of jobs it can complete — many stations may use low-volume or short-run productions for operation.
- Versatile modifications: Technicians can place the stations on flat surfaces, mount them on a cabinet with wheels or modify the circuit boards with other surface-mounted devices, including land grid arrays, column grid array packaging, quad flat packages and chip scale packages.
- Varied capabilities: A BGA rework machine allows technicians to complete several tasks, including reworking or refinishing components, repairing or removing defective parts, reinstalling parts into the correct placement, removing components that are no longer working and replacing any missing parts.
- Automated options: The machines may provide an automatic BGA rework station or partial automation capabilities with or without a connected PC, while others require manual labor based on the task and system.
- Camera assistance: A BGA rework machine may contain a split-vision assist camera, which allows for more complex work — stations without split-vision functionality are better for entry-level tasks.
- Self-containment: The machines include their own internal air and vacuum, so they're fully self-contained unless the product description specifies otherwise.
What Are the Benefits of BGA Rework Stations?
When deciding whether you should invest in BGA rework or reflow stations, consider their incredible advantages:
- Cost: The investment of a BGA rework station can offer a cost-effective solution compared to assembling or purchasing a new one. Reworking the machinery can produce a significantly longer PCB life span. The extended lifetime makes the upfront expenses more worthwhile.
- Volume: A BGA rework station can serve various sizes of PCBs. The machinery allows original equipment manufacturers and other companies to handle a high volume of rework jobs. Completing more rework services will enable you to serve more customers, increase revenue and accomplish your business-related goals.
- Efficiency: The BGA rework stations include highly specialized tools such as component pickup tubes, solder balls and nozzles. Proper training to use the tools and machinery ensures technicians have the skills and knowledge to correctly utilize these components during rework tasks. The tools allow technicians to increase their speed and complete work on a fast timeline.
- Accuracy: A technician can use the tools in a BGA rework station to complete skilled and detail-oriented tasks. The tools allow for safely and accurately completing many delicate processes, like reworking a ball grid array. With attention to detail and precision, technicians can complete reworking tasks without damaging the device.
Application Use for a BGA Rework Machine
BGA rework stations have several different applications in the world of PCB repair and alteration. Here are a few of the most common applications.
- Faulty assembly: A range of mistakes can occur during the rework process. For example, the PCB may have incorrect BGA orientation or a poorly developed BGA rework thermal profile. In this case, the PCB will likely need to undergo further rework to address the faulty assembly.
- Faulty parts: PCBs can have various defective parts that may require rework. While pads could get damaged during BGA removal, any number of components could be heat-damaged, or there could be too much solder joint voiding.
- Upgrades: Often, technicians complete reworks to upgrade various components. Professionals can replace a PCB's outdated or low-quality parts for improved quality, performance and longevity.
Hot Air vs. IR BGA Rework Stations
Original equipment manufacturers and PCB contract manufacturers typically use two different types of BGA rework stations: hot air or infrared (IR). What is the difference between these two types of BGA rework machine, and is one better than the other?
- Hot air BGA rework stations: Hot air BGA rework stations use hot air to heat up the PCB components during the project. Several different nozzles guide and circulate hot air to ensure even heat distribution. Technicians can move these nozzles to direct air, allowing work on small, delicate components to get accomplished quickly. The use of air pumps means there will be some level of noise when using a hot air BGA rework station, though many models can run very quietly. Because hot air is an older technology, more technicians have training in using hot air BGA rework stations as opposed to IR BGA rework stations.
- IR BGA rework stations: Instead of hot air, IR BGA rework stations use infrared rays and a fixed ceramic heater to heat PCB components. This type of rework station is completely silent. It also involves fewer pieces, which can make maintenance easier. However, depending on the quality of this machine, it may require more frequent maintenance and additional tools to accomplish the desired jobs. Since this is a newer technology, not as many technicians are trained to use IR BGA rework stations.
Both hot air BGA rework stations and IR BGA rework stations have pros and cons, but a big factor to consider is the skill of the technician operating the machine. Precision PCB Services focuses on hot air BGA rework stations because the technology is more firmly established.
Hot Air vs. Heat Guns
Hot air BGA rework stations offer many benefits, including air volume control and closed-loop temperature control. They provide greater precision and functionality than a heated gun.
On their own, heat guns or hot air wands don't usually include interchangeable nozzles. Because they aren't specifically designed for desoldering components, they pose the risk of overheating and damaging boards.
Why Precision PCB Services
Precision PCB Services offers a wide variety of different BGA rework stations to meet your needs, but the company also provides several other useful services.
- Consulting: Precision PCB Services offers consulting services to original equipment manufacturers, contract manufacturers and product development companies in the general PCB manufacturing industry, as well as in specialized industries like health care and aerospace. Rather than try to add BGA rework to your engineers' already full plates, trust dedicated, trained BGA rework specialists to handle the rework process. Our consulting services ensure you do not run into issues like incorrect BGA orientation, heat damage or pad damage.
If your company does its own BGA rework, Precision PCB Services' consulting team can help implement documented processes that will reduce waste, improve efficiency and boost yield. Thousands of engineers and technicians at many different manufacturing companies have used our BGA repair and rework consulting services.
- Training: Precision PCB Services has a variety of customized training courses designed to meet our customers' needs. Options include skills training, BGA rework, wiring and terminals, hand solder and rework, lead-free training, PCB repair, BGA reballing and more. We also offer on-demand classes for smaller groups of one to five people every day at our facility.
- Repair: Precision PCB Services also has repair services.
Precision PCB Services is also an authorized distributor and services center for Shuttle Star BGA rework stations.
If you have any questions about our products and services, or you are ready to buy a BGA rework station, contact us so we can help your business get what it needs to operate efficiently.
SRT Maintenance
SRT 1000, SRT Sierra, SRT Summit 1l00, SRT 1100HR BGA Rework Systems.
SRT - Training, Service, Maintenance, Calibration, Support and Computer Rebuilds.
Call us at Precision PCB Services, Inc. for all of your SRT requirements. Don't delay, call today!
- BGA Rework Training
- SRT Machine Calibration
- SRT Machine & Profile Set Up
- SRT Computer Repair, and hard drive replacement.
- Used machine sales.
- Machine installation and setup.
Shuttle Star Support
We are a Shuttle Star Distributor and provide a full array of support services for Shuttle Star BGA Rework Stations.
- Shuttle Star Sales
- Shuttle Star Technical Support
- Shuttle Star Profile Development
- Shuttle Star Training
- Shuttle Star Repair
- Shuttle Star Parts
- Shuttle Star Nozzles
R & D Support
At Precision PCB Services, Inc., we offer a full range of Specialized Product Development Support Services to help you get your product to market. Having worked with over 2000 engineers, managers, and executives at over 1000 companies. We bring a unique mixture of experiences that very few companies can provide.
Specialized in: High Tech, Advanced and Emerging Technologies. We can work with specialized chips from 5000 ball ceramic chips to fine pitch, Micro BGA Thin substrates, low heat considerations, piggy backing, chip stacking, encapsulation and more.
- Circuit Modification.
- Defect Analysis.
- Design for Manufacturing.
- Manufacturing Process Development.
- Specialized Equipment.
- Specialized Tooling and Fixturing.
- Solder Balling and Solder Bumping of BGA, QFN, LGA
- Stencils and Solder Pastes for fine pitch paste printing.
- Surface Finish Analysis.